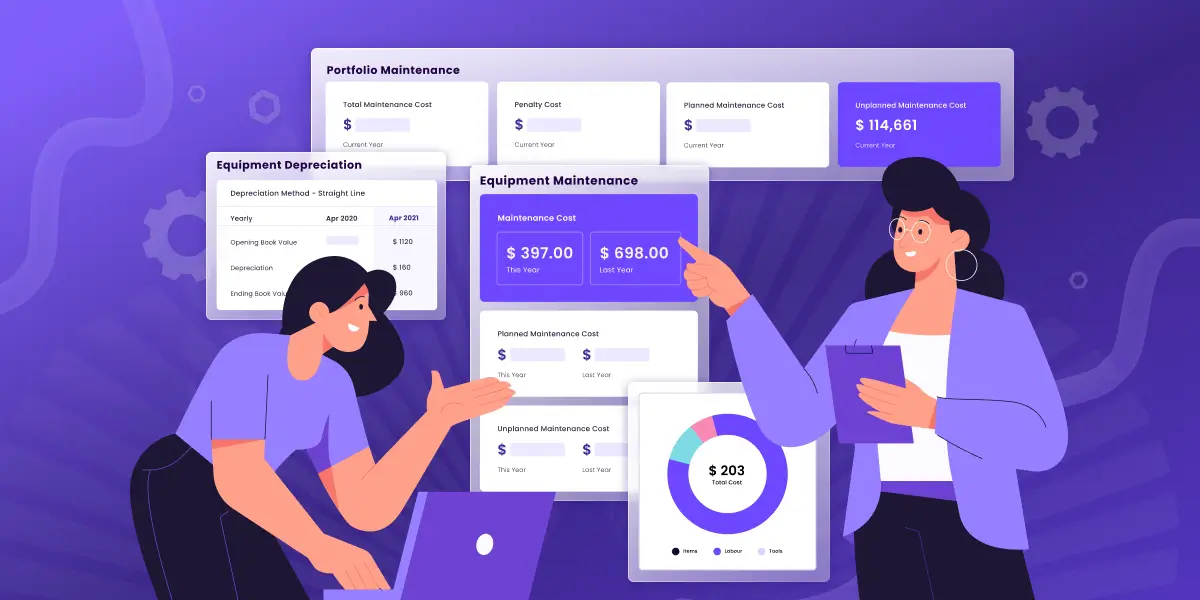
Let’s face it—facility management is challenging primarily because of unforeseen issues with assets and personnel. These problems are further intensified by the absence of digital processes and an excessive dependence on manual processes to resolve them.
Manual processes not only impede company operations but also lead to the nightmare of managing spreadsheets, long threads of email follow-ups, and paperwork, resulting in reactive management, which is no longer suitable in today’s competitive market. Relying alone on a 'run-to-failure, then fix it' strategy won’t cut it.
This has heightened the urgency to bring planned predictive maintenance practice into the DNA of facility operations to minimize downtimes and provide an extraordinary occupant experience. Adopting planned maintenance systems (PMS), especially those emphasizing automation, can effectively address these issues.
So, for a comprehensive understanding, this article will focus on guiding the transition to more planned maintenance with PMS, what to look for in quality PMS, and illustrate real-life cases of how a PMS is successfully employed.
What is planned maintenance?
Planned maintenance is a proactive maintenance strategy to keep your facility and operational machinery running smoothly. Sometimes referred to as preventive maintenance, it involves careful planning, documenting, and scheduling of every possible maintenance task that improves asset lifetime and performance.
The whole point? To slash downtime and improve asset/facility uptime as quickly as possible by having all the heavy hitters running efficiently across the portfolio.
Assets wear out; that’s a given. However, planned maintenance is how maintenance managers stay on top of things to ensure efficient operation throughout the asset’s lifecycle.
To nail effective planned maintenance, you would have to shift your facility management onto a computerized maintenance management system (CMMS). This tool streamlines your operations and frees you from the clutches of manual headaches. To learn more about how to move away from manual and broken processes, check out our webinar.
In 2021, a survey found that preventive maintenance was the most widely adopted strategy in the real-estate facility operation industry. 88% of participants reported implementing a preventive maintenance strategy, with only 52% still opting for reactive maintenance.
Suggested read: How to develop a planned maintenance plan
What are the different types of planned maintenance systems?
There are four major types of PMS. This categorization, however, is not a static framework; it adapts to the unique challenges confronted by facility managers or O&M teams within their respective companies. Also, the practicality of each type becomes apparent based on how the PMS functions.
Let’s take a look.
Usage-based preventive maintenance
This PMS strategy allows you to track an asset's usage patterns to predict the next inspection or maintenance based on its operational history.
Practical planned maintenance example - Healthcare
Facility management (FM) teams can leverage usage-based preventive maintenance to keep hospital operations in optimal condition.
X-ray machines:
- Maintenance work:
- Regular calibration checks
- Inspection of imaging components
- Output:
By adjusting the maintenance schedule based on recurrent data from the number of scans or the cumulative radiation exposure.
This type of proactive maintenance lets the hospital ensure that crucial services, like diagnostic imaging or life-support systems, are consistently available to patients. This reliability builds trust among patients and their families as they experience uninterrupted healthcare services.
Predictive maintenance
Predictive maintenance is rooted in continuously monitoring asset conditions by leveraging sensors and data analytics to detect patterns that may indicate impending failures.
This approach is well-suited for high-value assets where unexpected downtime can result in significant financial losses or operational disruptions.
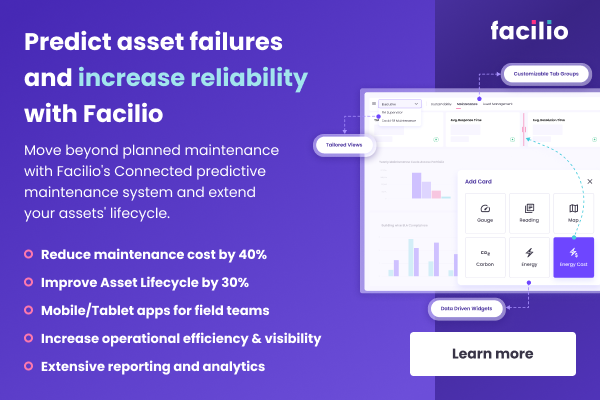
Practical planned maintenance system example - Retail setups
Refrigeration systems:
- Maintenance work:
- Continuous monitoring of compressor efficiency
- Refrigerant level checks
- Output:
By analyzing real-time data on compressor performance, potential issues can be identified and addressed before they lead to system failures. This would help in preserving perishable goods and preventing revenue loss.
The proactive nature of predictive maintenance minimizes the likelihood of disruptions and creates a smoother shopping experience. Uninterrupted functionality of essential systems like refrigeration prevents inconvenience, ensuring customers enjoy their time at the retail store.
Time-based preventive maintenance
This type of PMS is suitable for assets that require regular upkeep at fixed intervals. It relies on calendar schedules to plan and organize maintenance tasks efficiently. Once the due date approaches, maintenance actions are initiated, and work orders are automatically generated.
Practical planned maintenance system example - Commercial real estate
Fire sprinkler systems:
- Maintenance work:
- Periodic testing and inspection
- Output:
Scheduled time-based maintenance could ensure that fire sprinkler systems are always in proper working conditions. This takes care of the overall fire safety within the commercial property.
This PMS strategy in commercial real estate minimizes the risk of unexpected breakdowns, all to make sure that occupants experience a consistently safe and comfortable environment. Regular maintenance also contributes to the longevity of building assets, reducing the likelihood of major mishaps that could upset tenants.
According to a report by Plant Engineering, around 9% of equipment downtime results from a lack of time for maintenance. More attention paid to time-based preventive maintenance could see a noticeable reduction in downtime accumulation.
Prescriptive maintenance
This type of maintenance approach goes beyond predicting a failure; it also seeks the reasons. This type of maintenance is suitable for environments with a wide range of facilities.
Practical planned maintenance system example - Universities
Laboratory equipment:
- Maintenance work:
- Equipment performance analysis
- Identification of components showing signs of degradation
- Output:
Prescriptive maintenance would help universities understand why laboratory equipment may fail. This allows precise and targeted interventions to replace worn-out parts and prevent disruptions to critical research activities.
This precision is vital for ensuring the reliability of specialized equipment, directly impacting research, teaching, and overall campus efficiency.
How a planned maintenance system works to improve system reliability
Planned maintenance systems improve system reliability by leveraging operational data analytics and predictive asset monitoring. At Facilio, we take it a step further by utilizing machine learning and AI to transform maintenance strategies with a heavy focus on automation.
Here’s how maintenance managers can implement planned management software to increase asset reliability:
Related Read: Top 10 Best CMMS Software
Centralized control with CMMS
As an integral component within the CMMS framework, the planned maintenance system functions as a centralized platform, providing oversight and control over critical maintenance actions and tasks.
Facilio excels here by optimizing CMMS positioning. This prioritizes seamless team communication, enhances the workflow engine, strategically allocates resources, and efficiently synchronizes work orders.
Reduce reliability risks
PMS offers valuable insights into asset conditions. This allows maintenance managers to proactively identify and address potential issues before they impact equipment reliability and productivity.
Task prioritization
PMS allows you to prioritize maintenance tasks based on criticality and urgency. High-priority tasks are given more attention, minimizing downtime more effectively.
Cost management
You can generate detailed reports on the costs associated with the asset maintenance activities using a PMS. For example, Facilio’s portfolio maintenance section offers a dashboard for managers to monitor expenditures, compare prices against budgets, and implement better strategies to optimize budgets and reduce overall expenses.
Let’s look at two notable case studies at Facilio, where our planned management systems have improved asset reliability for our clients.
Case study #1: How Facilio revolutionized British Land’s property development with our connected buildings solution
To provide real-time analysis of energy consumption, visitor movement, and energy optimization opportunities, consider the use case of British Lands, a property development company.
British Land, a leading property development and investment powerhouse in the UK commands assets exceeding £14.1 billion, spanning state-of-the-art office spaces and retail outlets.
Determined to create 'places people prefer,' British Land strategically partnered with Facilio. Their goal was to centralize data, ensuring smooth accessibility for stakeholders across diverse portfolios.
Problem Areas:
- The functionality of digital tools was compartmentalized, impeding visibility at both property and portfolio levels
- Dependency on vendors for reporting introduced delays in real-time analytics, leading to deferred fault detection
- The absence of contextual information affected the ability to derive insights for optimizing assets
Solution:
Implemented Facilio’s Connected Buildings as an overlay platform to consolidate data and get real-time insights. The solution accommodated both Storey (co-working spaces) and Landlord (empty buildings) types, allowing British Land to integrate data from diverse tools and provide contextual insights.
Impact:
Our collaboration with British Land delivered impressive results. We slashed heating and cooling energy consumption by 50% year-over-year, enhancing occupant comfort and fine-tuning over 300,000 minutes of air conditioning operations.
Lear More on How British Land moves closer to net-zero operations with Facilio’s Connected Buildings
Case study #2: How Facilio helped Tutenlabs Inc. improve workflow and optimize operations
Prioritize critical alerts, enable remote troubleshooting, and deploy on-site staff promptly for optimal refrigeration and HVAC asset maintenance, as exemplified by Tutenlabs, a tech company.
Nestled in Atlanta, Georgia, Tutenlabs Inc. is a tech company specializing in helping retail shops trim energy use, cut emissions, and save costs.
Their goal was to remain a frontrunner in its industry by consistently delivering value and optimizing stakeholder savings.
Problem Areas:
- The absence of a centralized monitoring system led to alarm prioritization challenges and delayed service delivery
- Challenges in distinguishing critical and non-critical alarms resulted in alarm fatigue and sluggish response times
- Manual alarm reconciliation slowed down root cause analysis and corrective actions
- Human-led work order processes introduced inefficiencies and potential errors in the workflow
Solution:
Unified Monitoring + Maintenance & Streamlined Operations
Facilio's platform addressed alarm prioritization issues, reducing response times, and enhancing operational efficiency. This unified approach encompassed 24/7 predictive monitoring, proactive helpdesk services, centralized vendor management, and refrigeration optimization.
Impact:
Our collaboration with Tutenlabs resulted in a noteworthy 10-15% cut in service calls, meaning quicker fixes and big savings.
Thanks to our smart AI-driven system, alarms got smarter too, turning quick-fix data for smoother operations. Real-time insights from the platform improved service efficiency, keeping assets in top shape and making maintenance easy.
PMS software allows you to effortlessly take charge of your company. If you’re looking for actionable steps to ace your PMS routine, check out how to take control of your planned management system.
Learn More on How Tuten Labs Leverages Facilio to Digitize & Automate O&M across 10,000 Large Format Retail Stores
Key features to look for in a planned maintenance system
Preventive maintenance scheduling
Preventive maintenance (PM) scheduling is essential for keeping your assets in top-notch condition. It ensures regular check-ins to avoid unexpected breakdowns. With our PMS, you can effortlessly set up recurring maintenance tasks for each asset.
Whether it's time-based intervals or meter readings, configuring optimal schedules depends on the maintenance software you use.
Customizable and user-friendly interface
A good PMS should have a fluid, user-friendly interface. It will work to get your team to adapt to the system quickly. Customization ensures that the PMS aligns perfectly with your industry and the existing workflow, reducing resistance to change and accelerating the adaptation process.
With customization, you could tweak your PMS to fit any operational format without establishing a new system to accommodate new changes.
Facilio allows you to create a personalized dashboard and add elements like images, texts, or cards.
Comprehensive asset management
Making sure your PMS can smoothly track and document large asset portfolios in detail is an important feature.
Facilio, for instance, gives you information about the who, what, when, and where of every asset covered. With just a click, you can pull up an asset's entire life cycle story.
Below is a screenshot showing the address, building, and floor where the equipment (chiller) is located.
Work order management
One fundamental feature your PMS needs is work order management. It's non-negotiable. Your planned maintenance system should quickly create, assign, and hand out work orders.
The image below depicts a recurring work order set up for routine coolant checks. It displays the assigned person, the asset tracking number, and the pre-filled planned maintenance schedule spanning several months ahead.
Related Read: Best Work Order Management Software for Maintenance
Inventory order management
This involves overseeing the procurement, storage, and tracking of spare parts, materials, and supplies needed for maintenance.
Facilio's connected CMMS allows you to monitor your spares and replacements easily during asset maintenance. Each inventory item maintains a detailed usage history and work orders it's been part of.
It has a streamlined process of generating requests for quotations and purchase requests within the inventory order management system.
Downtime tracking
Equipment downtime tracking allows you to understand how often things go haywire and how long they take a breather when they do.
This gives the maintenance manager a headstart on information. You can explore other alternatives or get repairs early on to avoid taking big hits and accumulating downtime.
KPI dashboards
The planned maintenance system should provide access to key performance indicators (KPIs). These KPIs allow you to make informed decisions about the necessary adjustments to current practices.
PMS Evolution: Facilio’s Tech-Infused Approach
The impact of tech advancements on innovation is breaking new heights. And at Facilio, we're right in the thick of it. Our commitment shines through in our moves to wield AI and ML, reshaping how we analyze data from different systems.
Facilio's contribution to PMS: What sets Facilio apart
Optimized automation in workflow engine
Many PMS software solutions fail to address comprehensive O&M needs. Cumbersome manual processes and limited digitization can pose significant limitations. Facilio, however, takes a different route. We leverage advanced digital solutions and focus on O&M automation to ease the load and save valuable time.
Modern codebase for easy updates and integrations
Certain maintenance systems rely on outdated codebases dating back 20-25 years, making them operate as standalone rigid systems.
Facilio, in contrast, is built on more recent codebases, granting it adaptability to evolving needs and encouraging integration.
360° bird’s eye view on asset management
With this Facilio feature, the maintenance team gets the whole picture right within the system—keeping tabs on maintenance tasks, resources, and performance metrics. On the flip side, many other maintenance systems miss out on this integrated view, constraining users to play interface hopscotch for insights.
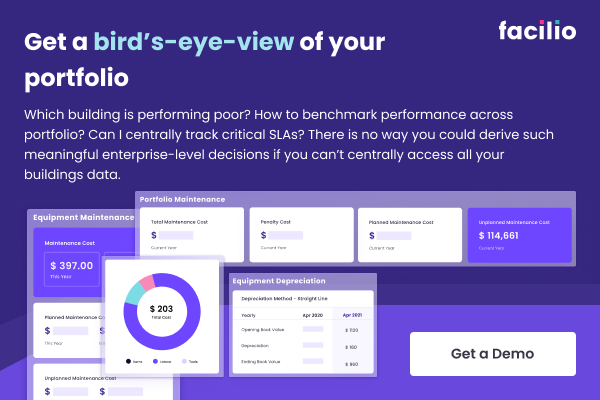
Increased mobility
Unlike other PMS software that often restricts mobility, mostly relying on desktop web versions, Facilio breaks free with accessibility in mind. With both web and mobile versions at your disposal, you can manage maintenance tasks whether you're at your desk or on the move.
Conclusion
Here’s the thing: deferring proactive asset maintenance might seem like a cost-saving move, but it's a gamble. The longer you wait, the higher the odds of equipment breakdowns and decreased efficiency. Sure, you might save a few bucks initially, but is it worth the risk of things going south?
This is where planned maintenance systems come in. It helps with routine checks, automates workflows, and acts as a proactive shield against unexpected disruptions at your facility that may cause downtimes.
But, and it’s a big one, choosing the right PMS provider is the game-changer.
While features are very important, you also need to find a partner that understands your company's needs and the operational mishaps you are looking to fix.
Don’t roll the dice on reactive maintenance. Invest wisely in a PMS that puts you in control. Here at Facilio, we’ll put you at the helm of all your maintenance operations. Book a Demo.