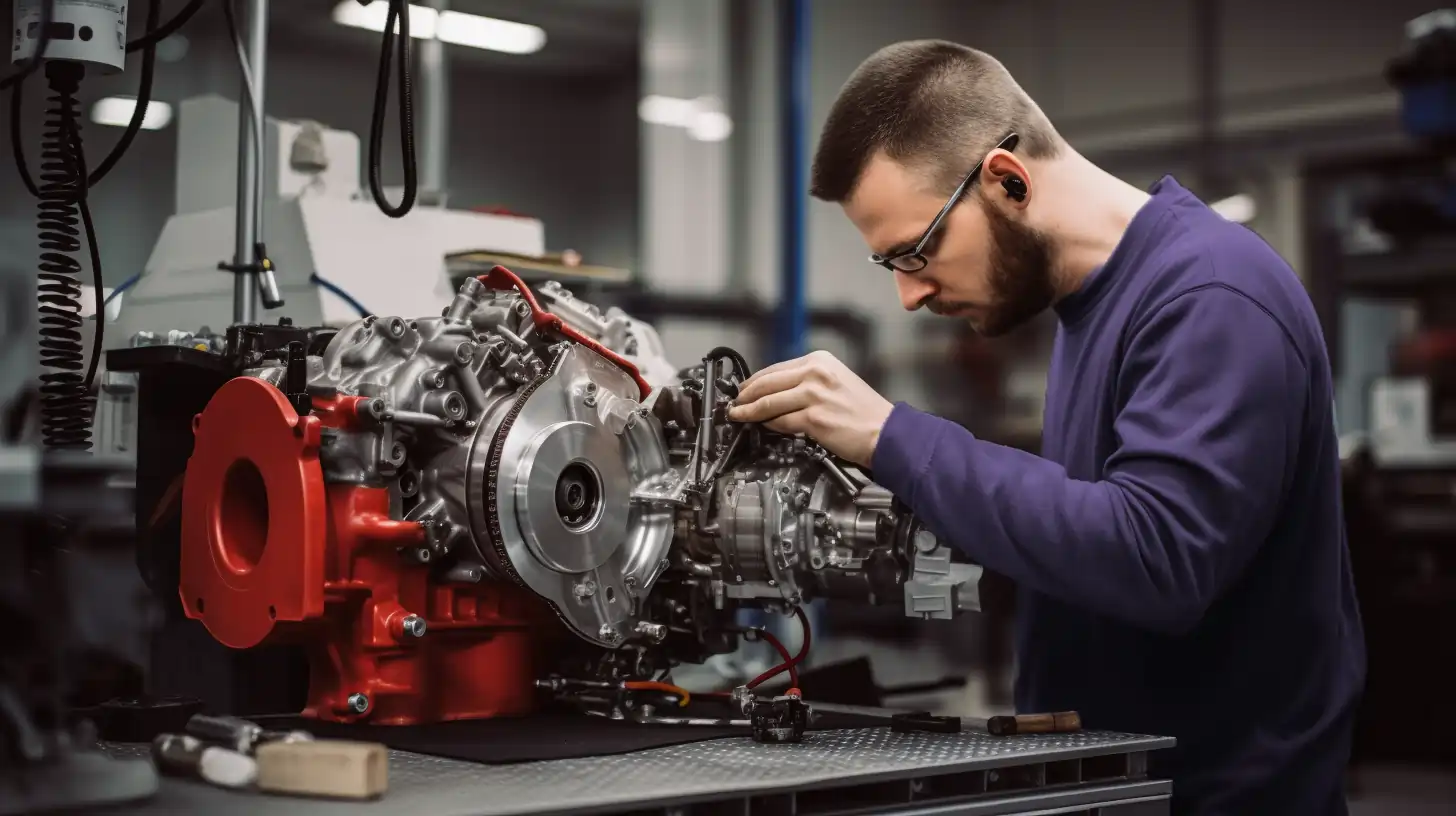
In the maintenance world, we've got two big players: reactive maintenance and preventive maintenance. Each has its own pros and cons, so it's crucial for businesses to grasp the core differences and make a smart call.
In this article, we'll dive into maintenance basics, define reactive and preventive maintenance, break down their advantages and disadvantages, and give you the scoop on choosing the right strategy for your business.
TL;DR
Reactive maintenance provides immediate cost savings but raises the risk of downtime and premature equipment failure. Preventive maintenance, while entailing higher upfront costs, leads to long-term savings by proactively addressing issues and optimizing equipment performance.
The decision should be based on factors such as equipment criticality, downtime costs, and available resources, with the option of a hybrid approach for optimized efficiency and reduced costs.
What is Reactive Maintenance?
While reactive maintenance might work well for certain situations, like handling minor repairs or non-critical equipment issues, it's not the best long-term game plan.
Relying solely on reactive maintenance can hike up costs, reduce productivity, and raise the chances of equipment failures. It's crucial for businesses to carefully weigh the impact of reactive maintenance on their operations and think about incorporating preventive measures to cut down on risks.
Bringing in a computerized maintenance management system (CMMS) can be a game-changer for handling reactive maintenance. A CMMS helps keep tabs on maintenance requests, prioritize tasks, and make sure the necessary resources are ready to tackle issues ASAP.
With a CMMS in play, businesses can streamline their reactive maintenance processes and boost overall efficiency.
Book a demo and learn more about how Facilio's connected CMMS can optimize maintenanace across your portfolios
What is Preventive Maintenance?
Preventive maintenance includes activities like lubrication, cleaning, calibration, and parts replacement, guided by manufacturer recommendations, industry standards, and historical data analysis.
Following a well-defined plan ensures equipment operates at peak performance, minimizing breakdown risks and extending its lifespan.
Key Advantages:
- Scheduled Maintenance: Allows businesses to schedule activities during planned downtime, minimizing production impact.
- Resource Optimization: Enables efficient allocation of resources.
- Issue Identification: Helps identify and address minor issues before they become major problems, saving time and money.
Implementation Steps:
- Planning: Create a comprehensive maintenance schedule.
- Responsibility Assignment: Assign responsibilities to qualified personnel.
- Resource Readiness: Ensure necessary tools and spare parts are readily available.
- Training and Communication: Conduct regular training and communication to emphasize the importance of preventive machine maintenance and ensure adherence to established procedures.
The Core Differences Between Reactive and Preventive Maintenance
Now that we have defined the two approaches, let's delve deeper into their differences and explore the various factors that set them apart.
Approach to Maintenance Tasks:
- Reactive Maintenance: Immediate problem-solving with urgent repairs or replacements.
- Preventive Maintenance: Planned and preventive approach, with scheduled tasks based on equipment usage and manufacturer recommendations.
- Proactive Advantage: Preventive maintenance minimizes the risk of costly unplanned downtime.
Cost Implications:
- Reactive Maintenance: Initially more cost-effective, but potential for higher long-term costs.
- Preventive Maintenance: Higher initial costs but significant long-term savings by preventing breakdowns, extending equipment lifespan, and maintaining productivity.
Impact on Equipment Lifespan:
- Reactive Maintenance: Increased risk of premature equipment failure due to fixing problems as they arise.
- Preventive Maintenance: Aims to extend equipment lifespan by regularly inspecting and servicing, identifying and addressing potential issues early on.
Pros and Cons of Reactive Maintenance
Pros of Reactive Maintenance
- Immediate Cost Savings:
Focuses on necessary repairs, avoiding unnecessary maintenance expenses.
- Feasible for Limited Resources:
More feasible for businesses with limited resources due to minimal planning requirements.
Cons of Reactive Maintenance:
- Increased Risk of Downtime:
Equipment failures can lead to productivity loss, missed deadlines, and customer dissatisfaction.
- Lack of Regular Inspections:
Potential issues may go unnoticed until they become more extensive and expensive to repair.
- Safety Concerns:
Unplanned breakdowns may pose safety risks to personnel and assets.
- Shortened Equipment Lifespan:
Frequent reactive repairs can contribute to premature wear and tear.
Pros and Cons of Preventive Maintenance
Pros of Preventive Maintenance
- Minimization of Equipment Failures:
Regular inspections and servicing identify and resolve issues before they cause downtime.
- Extended Equipment Lifespan:
Long-term cost savings by preventing minor issues from evolving into major problems.
- Improved Safety:
Regular checks contribute to a safer working environment.
- Enhanced Predictability:
Predictable maintenance schedules allow for better planning and resource allocation.
Cons of Preventive Maintenance
- Coordination Challenges:
Balancing maintenance activities with production requirements requires effective planning and coordination.
Facilio tackles coordination challenges by providing a centralized platform that facilitates seamless communication and integrated scheduling.
Real-time updates and resource optimization tools ensure effective planning, allowing maintenance activities to align harmoniously with production requirements without causing disruptions.
- Potential Over-Maintenance:
There's a risk of performing unnecessary maintenance if not based on accurate usage and manufacturer guidelines.
Facilio mitigates the risk of over-maintenance by leveraging usage analytics, integrating manufacturer guidelines, and employing predictive analytics.
The dashboard analyzes actual equipment usage, ensuring maintenance interventions are based on accurate information. Integrating manufacturer guidelines prevents unnecessary maintenance, and predictive analytics forecasts maintenance needs based on real-time performance trends, preventing preemptive actions on non-existent issues.
Flexible, user-friendly Preventive maintenance management software that adapts to your needs - Facilio
Empower your team with the ability to efficiently manage maintenance tasks, providing a hassle-free experience tailored to your operational needs.
Choosing the Right Maintenance Strategy for Your Business
When it comes to maintenance strategies, there is no one-size-fits-all approach. Every business has unique operational requirements, budgets, and goals. Therefore, it is crucial to carefully consider various factors to determine the most suitable strategy.
Factors to Consider:
- Criticality of Equipment:
- Assess the significance of each piece of equipment to daily operations.
- Prioritize maintenance efforts based on the impact of potential failures on overall productivity.
2. Cost of Downtime:
- Quantify the financial impact of equipment failures and unplanned downtime.
- Consider how swiftly different maintenance strategies can get operations back on track.
3. Frequency of Failures:
- Analyze historical data to understand how often equipment breakdowns occur.
- Identify patterns and trends to anticipate potential problem areas and plan maintenance accordingly.
4. Available Resources:
- Take stock of the human and material resources available for maintenance.
- Assess the feasibility of implementing comprehensive preventive maintenance considering your resource capacity.
Scale your preventive maintenance with Facilio
Revolutionize your preventive maintenance approach with Facilio, a comprehensive facility management platform designed to scale seamlessly with your evolving needs. Facilio provides a centralized hub for preventive maintenance, allowing you to streamline tasks, enhance operational efficiency, and prolong the life of your assets.
Key Features:
#1 Customized Maintenance Scheduling:
Tailor preventive maintenance schedules based on equipment needs and operational priorities.
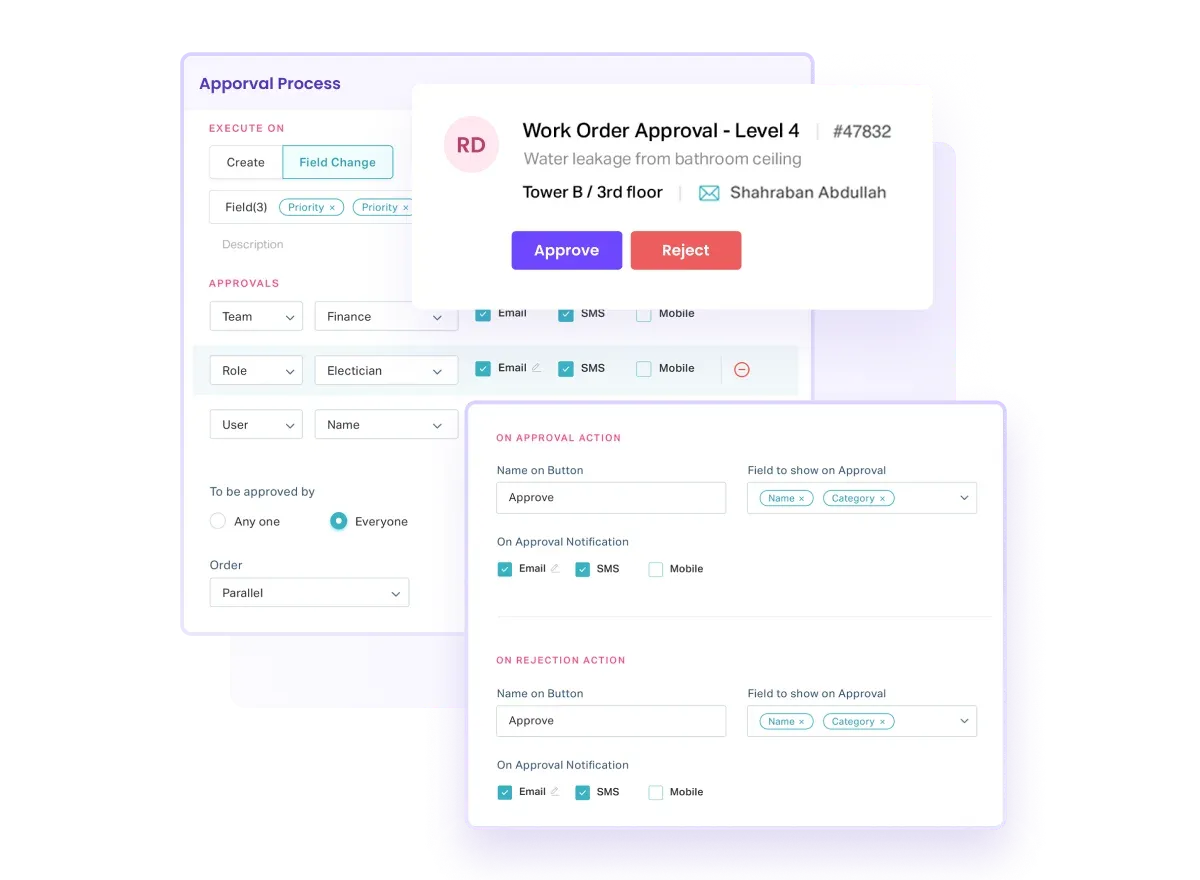
#2 Real-time Asset Monitoring:
View real-time insights into asset health, enabling proactive maintenance interventions.
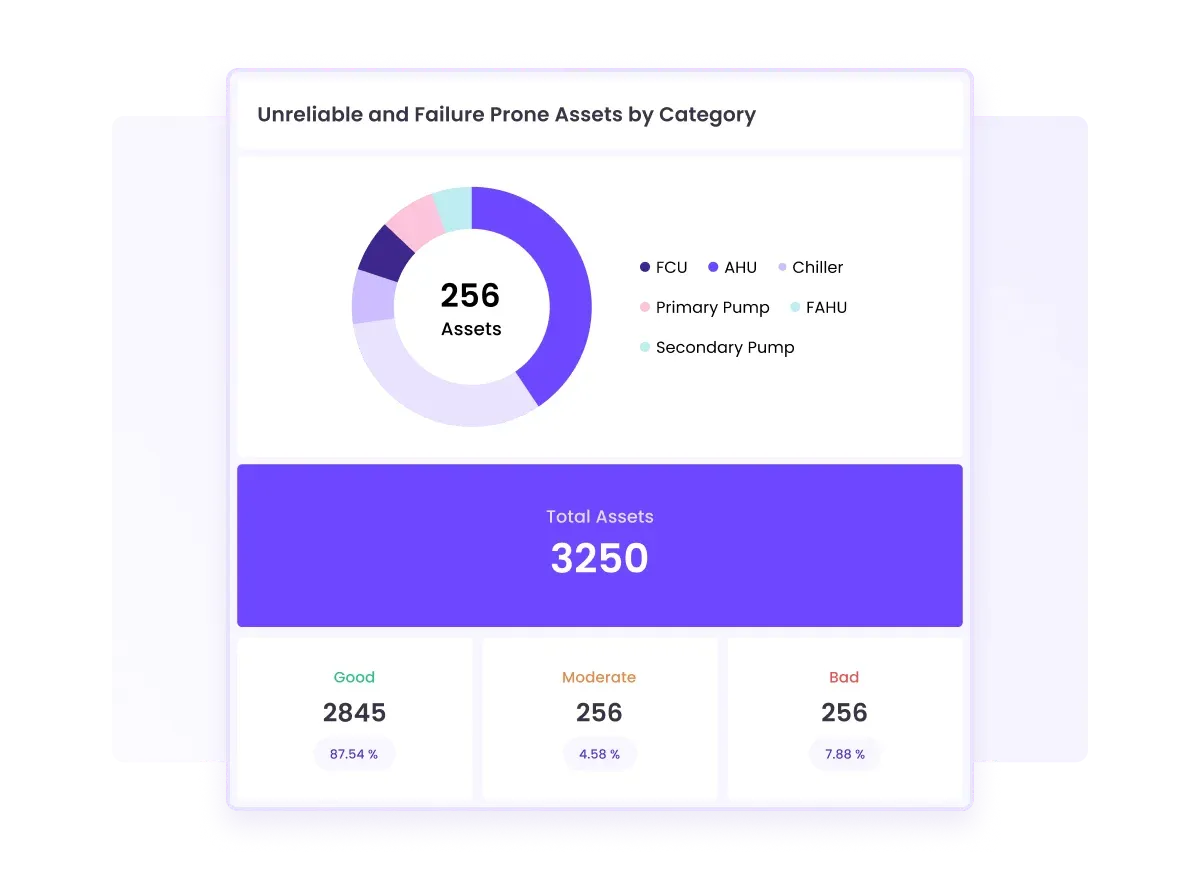
#3 Work Order Management:
Efficiently manage work orders, from creation to completion, ensuring a streamlined workflow for your maintenance team.
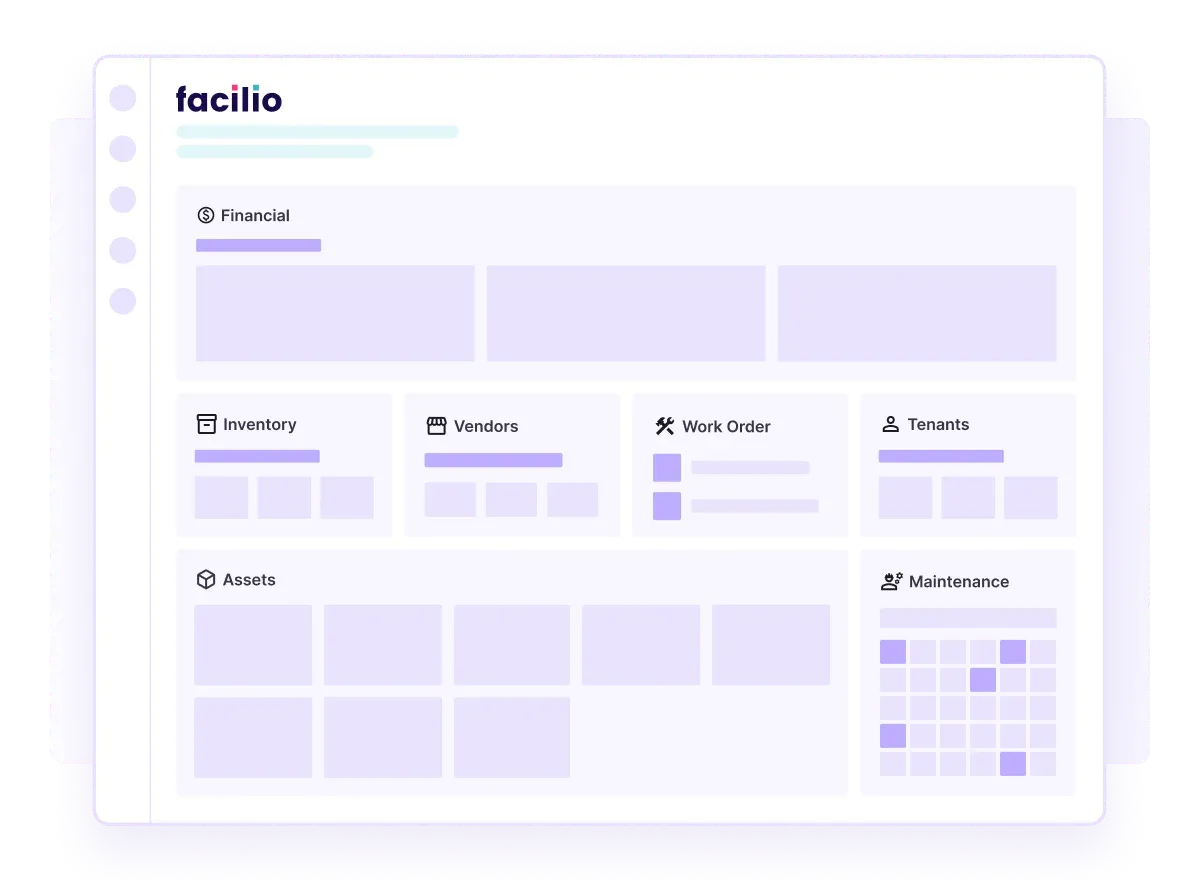
Interested to learn more?